Introduction
In the fast-paced and competitive world of manufacturing, KPIs in manufacturing in 2025 are essential for driving efficiency, ensuring quality, and maintaining profitability. As we approach 2025, the role of KPIs is becoming even more critical, with advancements in technology, automation, and data analytics reshaping how manufacturers track and optimize their operations. These performance metrics allow companies to monitor critical aspects of production, such as machine efficiency, product quality, and supply chain management, providing valuable insights that enable better decision-making.
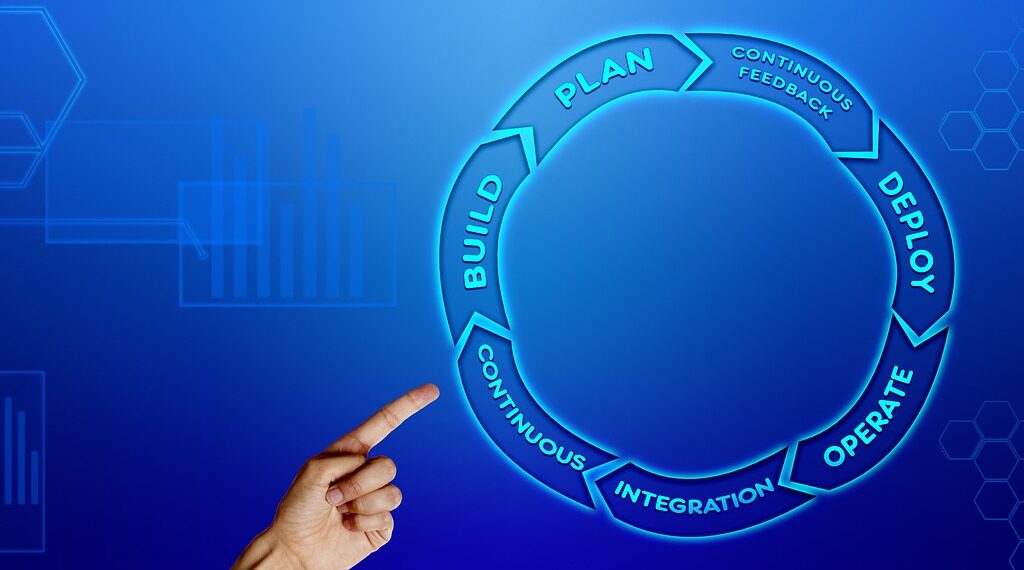
In recent years, the evolution of Industry 4.0 has introduced new tools and technologies—like IoT devices, AI-driven analytics, and real-time data monitoring—that have further transformed how KPIs in manufacturing in 2025 are measured and applied. Manufacturers today are not only focusing on traditional metrics, such as production output and defect rates, but are also adopting more sophisticated indicators related to predictive maintenance, sustainability, and workforce performance.
This blog will explore the key KPIs in manufacturing in 2025, the emerging trends in manufacturing performance measurement, and how companies can adapt to leverage these metrics effectively. By understanding and implementing the right KPIs, manufacturers can improve operational performance, enhance quality control, and remain competitive in an increasingly dynamic market.
The Evolution of Manufacturing KPIs
The evolution of manufacturing KPIs has been shaped by shifts in technology, market demands, and operational strategies. Traditionally, manufacturing KPIs focused on basic metrics such as production output, defect rates, and machine uptime. These were simple indicators that helped manufacturers assess their performance in terms of efficiency and product quality. However, as technology advanced, so did the complexity of KPIs.
In the early 2000s, the integration of Enterprise Resource Planning (ERP) systems allowed manufacturers to collect and analyze more granular data across various departments. This enabled more sophisticated KPIs, such as inventory turnover, order fulfillment cycles, and supply chain efficiency, to become central to operations. The rise of automation and robotics further influenced the development of KPIs, making machine efficiency and downtime tracking increasingly important.
By the 2010s, the advent of Industry 4.0 and the Internet of Things (IoT) revolutionized KPI tracking, allowing real-time data collection from machines, sensors, and connected devices. Predictive maintenance, energy efficiency, and workforce productivity began to emerge as crucial KPIs for manufacturers aiming for sustainability and cost reduction.

Looking ahead to 2025, manufacturing KPIs will continue to evolve, incorporating artificial intelligence, machine learning, and data analytics to drive smarter decision-making and enhanced performance.
Key Manufacturing KPIs for 2025
As we move toward 2025, Key Performance Indicators (KPIs) in manufacturing are evolving to address the increasing complexity of operations and the growing reliance on digital technologies. These KPIs will be crucial for optimizing production, reducing costs, ensuring quality, and driving sustainability. Below are 10 essential manufacturing KPIs that will shape the industry in 2025:
- Overall Equipment Effectiveness (OEE): OEE is a comprehensive measure of manufacturing efficiency, assessing availability, performance, and quality. By 2025, real-time data from IoT devices will provide more precise insights into equipment performance, helping to reduce downtime and improve production efficiency.
- Cycle Time: This KPI measures the time it takes to produce a unit from start to finish. In 2025, cycle time will be monitored closely using automated systems, providing data that can help streamline workflows and improve production speed.
- Throughput: Throughput refers to the number of units produced in a given period. It will remain a key KPI for evaluating how well a production line is performing, with real-time tracking offering manufacturers opportunities to optimize processes.
- Defects Per Million Opportunities (DPMO): Quality control will remain a top priority. DPMO measures the number of defects in a given production process and helps identify areas for improvement in quality assurance.
- First Pass Yield (FPY): FPY measures the percentage of products produced without rework or defects on the first attempt. Achieving high FPY rates will be critical for minimizing waste and reducing costs, making this KPI more important in 2025.
- Predictive Maintenance Metrics: Predictive maintenance leverages data from sensors and AI to predict when machines will need maintenance. By analyzing data such as vibration levels and temperature, manufacturers can avoid unplanned downtime, reduce repair costs, and extend equipment life.
- Energy Consumption Per Unit of Production: As sustainability becomes a key driver, tracking energy efficiency will be vital. This KPI measures how much energy is consumed to produce each unit of output, helping manufacturers identify areas to reduce energy usage and carbon footprints.
- Inventory Turnover Ratio: This KPI measures how often inventory is sold and replaced over a period. High turnover indicates efficient inventory management, while low turnover may signal overstocking or inefficiencies in the supply chain. In 2025, manufacturers will rely on real-time data to optimize inventory levels.
- Order Fulfillment Cycle Time: This KPI tracks how long it takes from receiving an order to delivering the product. Reducing order fulfillment time will be critical for meeting customer demands and maintaining a competitive edge in the market.
- Labor Productivity: As automation increases, labor productivity will remain important for assessing the effectiveness of human workers in a more automated environment. This KPI measures the output per employee or per hour worked, helping manufacturers assess the balance between human and machine contributions.
Emerging KPIs Driven by Industry 4.0
The rise of Industry 4.0 is driving the emergence of new Key Performance Indicators (KPIs) in manufacturing, thanks to technologies like IoT, Artificial Intelligence (AI), machine learning, and real-time data analytics. Here are some key emerging KPIs:
- Predictive Maintenance: By utilizing IoT sensors and AI algorithms, manufacturers can monitor equipment health in real time and predict when maintenance is needed, reducing unplanned downtime and extending equipment lifespan.
- Overall Equipment Efficiency (OEE): OEE tracking is becoming more dynamic, with real-time data from connected devices allowing for faster responses to equipment inefficiencies or failures, leading to better machine performance.
- Energy Efficiency: Manufacturers are increasingly focusing on energy consumption per unit of production. Real-time data helps optimize energy use, reducing both costs and environmental impact, while improving sustainability.
- Supply Chain Resilience: Real-time tracking of inventory, materials, and logistics helps manufacturers evaluate the flexibility and efficiency of their supply chains, enabling quick adaptations to disruptions or changes in demand.
These emerging KPIs highlight the role of data-driven insights in optimizing manufacturing performance and aligning with the principles of Industry 4.0.
How to Implement KPIs in Your Manufacturing Facility
Implementing KPIs in your manufacturing facility requires a strategic approach to ensure that the right metrics are tracked and that they align with your business goals. Here’s a step-by-step guide to help you effectively implement KPIs in your operations:
- Identify Key Objectives: Start by clearly defining the objectives you want to achieve. Are you focusing on improving efficiency, reducing downtime, enhancing product quality, or increasing sustainability? Your KPIs should reflect these goals, whether it’s improving OEE, tracking energy efficiency, or optimizing supply chain performance.
- Select Relevant KPIs: Choose KPIs that directly measure progress toward your objectives. For example, if reducing downtime is a priority, focus on Predictive Maintenance and Machine Uptime. If quality is key, prioritize First Pass Yield (FPY) and Defects Per Million Opportunities (DPMO).
- Leverage Technology: Use technology to collect real-time data from equipment, production lines, and supply chains. IoT sensors, ERP systems, and AI-driven analytics tools can help automate data collection, making KPI tracking more accurate and timely.
- Set Clear Targets: For each KPI, define specific, measurable targets. For example, aim to reduce cycle time by 10% or increase OEE to 85%. These targets will provide a clear benchmark for performance.
- Monitor and Analyze Data: Continuously monitor the KPIs, analyzing the data to identify trends and areas for improvement. Regular reviews of KPI performance will help identify bottlenecks, inefficiencies, or areas that need attention.
- Continuous Improvement: Use KPI insights to drive continuous improvement. When KPIs fall short, make adjustments to processes, provide employee training, or upgrade equipment to achieve desired outcomes.
Challenges in Tracking and Analyzing KPIs
Tracking and analyzing KPIs in manufacturing can be challenging due to various factors, especially as the complexity of operations increases with technology and automation. Some of the key challenges include:
- Data Accuracy and Reliability: One of the most significant hurdles is ensuring the data used for KPIs is accurate. Faulty sensors, data entry errors, or misaligned systems can result in misleading metrics, leading to poor decision-making.
- Integration of Systems: In many manufacturing facilities, different software and technologies (e.g., ERP, MES, and IoT devices) are used to track various KPIs. Integrating these systems seamlessly can be a complex and time-consuming process, making it difficult to get a unified view of performance.
- Real-time Data Collection: For KPIs like OEE or Predictive Maintenance, real-time data is essential. However, gathering and processing real-time information from connected devices or sensors can be technically challenging and costly, especially if infrastructure isn’t built to handle large volumes of data.
- Employee Engagement: KPIs are only effective if the entire team understands and actively engages with them. Resistance to change or a lack of training can lead to low adoption of KPI-driven processes, reducing their impact on performance.
- Continuous Monitoring and Adjustment: Manufacturing environments are dynamic, so KPIs need to be continuously monitored and adjusted to reflect changing goals, technologies, and market conditions. Failing to do so can result in outdated metrics that no longer align with business priorities.
These challenges highlight the need for careful planning, investment in the right technologies, and a proactive approach to KPI management.
The Future of KPIs in Manufacturing
The future of Key Performance Indicators (KPIs) in manufacturing is set to evolve significantly, driven by advances in technology, automation, and data analytics. As Industry 4.0 continues to reshape the manufacturing landscape, KPIs will become more dynamic, data-driven, and predictive, enabling manufacturers to make smarter, more informed decisions. Here’s a look at how KPIs will change and what manufacturers can expect moving forward.
- Increased Automation and Real-Time Monitoring: With the growing reliance on automation, the ability to track KPIs in real time will become even more important. Sensors, IoT devices, and advanced monitoring systems will continuously capture data from machines, production lines, and inventory, enabling real-time KPI tracking. Overall Equipment Effectiveness (OEE) and Predictive Maintenance metrics, for instance, will be more accurate, helping manufacturers prevent downtime and optimize machine performance instantly.
- AI and Machine Learning-Driven Insights: Artificial Intelligence (AI) and machine learning algorithms will revolutionize KPI tracking by automating data analysis and providing predictive insights. AI will not only help analyze vast amounts of data but will also identify patterns and trends that may go unnoticed by human operators. This capability will enable predictive KPIs, such as forecasting machine failure or demand fluctuations, improving decision-making and operational efficiency.
- Integration of Sustainability Metrics: As sustainability becomes an increasing focus for manufacturers, energy efficiency, waste reduction, and carbon footprint will become essential KPIs. The integration of sustainable manufacturing metrics into the KPI framework will not only help companies meet regulatory standards but will also align with consumer demand for eco-friendly products and processes. Manufacturers will leverage real-time data to optimize energy consumption, reduce waste, and track their environmental impact more effectively.
- Employee-Centric KPIs: As automation increases, there will be a stronger emphasis on workforce performance and engagement. KPIs such as labor productivity, employee engagement, and training effectiveness will be increasingly important. Rather than focusing solely on machine performance, manufacturers will track how employees interact with automated systems and contribute to overall performance. KPIs will be used to monitor employee satisfaction and retention, fostering a more engaged and productive workforce.
- Advanced Supply Chain KPIs: The future of manufacturing KPIs will also see a transformation in supply chain management. Supply Chain Resilience and Inventory Turnover will become more data-centric, leveraging AI and real-time data from IoT devices to predict and mitigate disruptions. With global supply chains becoming more interconnected and vulnerable to external factors, manufacturers will use KPIs to monitor not only their internal processes but also external variables, such as supplier performance and geopolitical risks.
- Customizable and Flexible KPIs: In the future, KPIs will become more adaptable to the specific needs of different industries and manufacturing types. Rather than relying on a one-size-fits-all approach, manufacturers will tailor their KPIs to reflect their unique processes, goals, and challenges. Cloud-based platforms and digital dashboards will allow manufacturers to adjust their KPIs quickly and efficiently as market conditions or business objectives change.
Conclusion
In conclusion, KPIs in manufacturing will continue to play a vital role in driving efficiency, improving product quality, and ensuring long-term profitability. As we move into 2025, the manufacturing landscape will be shaped by technological advancements such as automation, AI, IoT, and real-time data analytics. These innovations will enhance the accuracy, timeliness, and relevance of KPIs, enabling manufacturers to make more informed, data-driven decisions.
The integration of predictive analytics, sustainability metrics, and workforce performance indicators will further refine the way KPIs are used, making them more dynamic and reflective of modern manufacturing priorities. Real-time tracking, coupled with AI-powered insights, will empower manufacturers to proactively address issues before they impact production, reducing costs and improving overall performance.
However, successfully implementing and leveraging these advanced KPIs requires careful planning, investment in the right technologies, and a strong commitment to data accuracy. By selecting the right KPIs, integrating systems effectively, and fostering employee engagement, manufacturers can unlock the full potential of their operations.
As the manufacturing industry continues to evolve, KPIs will remain a crucial tool for driving growth, staying competitive, and adapting to new challenges. In embracing these emerging trends, manufacturers will be well-positioned for success in an increasingly digital and sustainable future.