KPI in manufacturing
In the realm of manufacturing, staying on track and achieving goals requires a clear compass. This is where Key Performance Indicators (KPIs) come into play. KPIs are like navigational tools that help businesses gauge their performance, ensuring that they’re headed in the right direction.
These measurable metrics provide valuable insights into various aspects of manufacturing, such as efficiency, quality, production, and costs. By focusing on KPIs, manufacturers can make informed decisions, identify areas for improvement, and enhance overall operations.
What is KPI in General
A Key Performance Indicator (KPI) is a measurable value that shows how effectively a company is achieving its key business objectives. KPIs are used to track progress, manage performance, and make informed decisions across various areas such as finance, marketing, operations, and more.
What is KPI in manufacturing
In the context of manufacturing, a Key Performance Indicator (KPI) is a quantifiable metric used to evaluate the efficiency, effectiveness, and overall performance of various aspects of the manufacturing process. These metrics are essential for assessing the success of manufacturing operations and ensuring alignment with business goals.
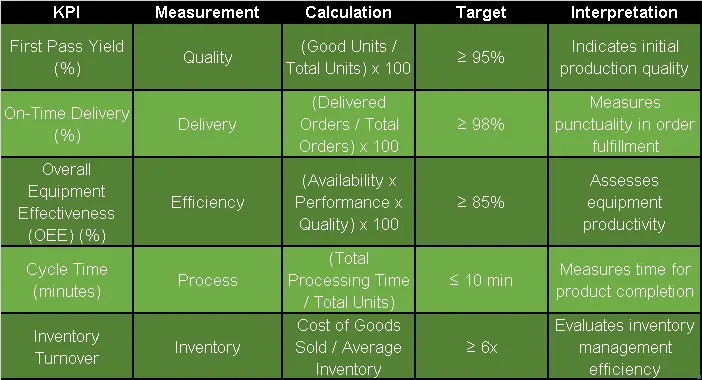
Manufacturing KPIs can encompass a wide range of factors, including production output, quality control, equipment downtime, inventory levels, and production cycle times. By tracking these indicators, manufacturers can identify strengths, weaknesses, and areas needing improvement. KPIs empower decision-makers to make data-driven choices that optimize processes, reduce costs, enhance productivity, and maintain product quality.
They serve as crucial tools in maintaining competitiveness and achieving sustainable growth in the dynamic landscape of manufacturing.
Quality KPI in manufacturing
Quality Key Performance Indicators (KPIs) in manufacturing are measurable metrics that gauge the standard of produced goods. These indicators encompass factors like product defects, rejection rates, and customer satisfaction levels. By tracking these KPIs, manufacturers ensure their products meet or exceed established quality standards, resulting in improved customer trust, reduced rework, and enhanced overall operational efficiency.
KPI in manufacturing example
KPI | Measurement | Calculation | Target | Interpretation |
---|---|---|---|---|
First Pass Yield (%) | Quality | (Good Units / Total Units) x 100 | ≥ 95% | Indicates initial production quality |
On-Time Delivery (%) | Delivery | (Delivered Orders / Total Orders) x 100 | ≥ 98% | Measures punctuality in order fulfillment |
Overall Equipment Effectiveness (OEE) (%) | Efficiency | (Availability x Performance x Quality) x 100 | ≥ 85% | Assesses equipment productivity |
Cycle Time (minutes) | Process | (Total Processing Time / Total Units) | ≤ 10 min | Measures time for product completion |
Inventory Turnover | Inventory | Cost of Goods Sold / Average Inventory | ≥ 6x | Evaluates inventory management efficiency |
Advantages of KPI in manufacturing
Performance Measurement:
KPIs offer a clear and quantifiable way to measure performance, helping manufacturers track progress toward specific goals and objectives.
Data-Driven Decisions:
KPIs provide real-time data that enables informed decision-making, allowing manufacturers to identify trends, patterns, and areas needing improvement.
Goal Alignment:
KPIs ensure that manufacturing activities are aligned with business objectives, helping teams stay focused on strategic priorities.
Process Optimization:
By monitoring KPIs, manufacturers can identify inefficiencies, bottlenecks, and areas for process improvement, leading to enhanced operational efficiency.
Quality Control:
Manufacturing KPIs related to defects and quality allow quick detection of issues, leading to timely corrective actions and improved product quality.
Resource Allocation:
KPIs help allocate resources effectively by highlighting where resources are most needed, optimizing production schedules, and reducing waste.
Continuous Improvement:
Regularly tracking KPIs fosters a culture of continuous improvement, promoting innovation and agility within manufacturing processes.
Competitive Advantage:
Using KPIs strategically can lead to increased competitiveness, as manufacturers can identify market trends and adapt their strategies accordingly.
Communication and Accountability:
KPIs provide a common language for communication among teams and stakeholders, fostering accountability and collaboration.
Benchmarking:
Comparing KPIs against industry standards or competitors offers insights into a manufacturer’s relative performance and areas for potential growth.
Challenges in KPI in manufacturing
Data Accuracy:
Ensuring accurate and reliable data collection can be challenging due to various data sources and potential inaccuracies.
Choosing Relevant KPIs:
Selecting KPIs that truly reflect business objectives and manufacturing processes is crucial but can be complex.
Setting Realistic Targets:
Establishing achievable KPI targets requires a balance between ambitious goals and practical expectations.
Integration Complexity:
Integrating KPI tracking systems with existing manufacturing processes and technologies can be intricate.
Change Management:
Implementing KPIs may require changes in workflows and employee habits, necessitating effective change management strategies.
Data Overload:
Monitoring numerous KPIs simultaneously can lead to information overload and hinder decision-making.
Contextual Interpretation:
Properly interpreting KPIs in the context of manufacturing operations requires a deep understanding of the industry and processes.
Employee Engagement:
Ensuring employee buy-in and engagement with KPIs is essential for successful implementation and utilization.
Continuous Review:
Regularly reviewing and adjusting KPIs to remain relevant and aligned with evolving business goals can be demanding.