What is manufacturing ERP system?
A manufacturing ERP (Enterprise Resource Planning) system is a comprehensive software solution designed to streamline and optimize the management of various processes within a manufacturing organization. This system integrates multiple functions, such as inventory management, production planning, scheduling, purchasing, sales, and financial management, into a centralized platform.
Furthermore, a manufacturing ERP system facilitates efficient communication and collaboration between different departments, enabling them to work in sync. By automating manual tasks and providing real-time data, it helps eliminate errors and reduce operational costs.
Additionally, it offers valuable insights into production efficiency, resource utilization, and supply chain management, allowing for informed decision-making
Moreover, the system’s ability to track and trace products throughout the manufacturing process ensures compliance with quality standards and regulations.
It enables businesses to optimize inventory levels, minimize stockouts, and improve customer satisfaction. Additionally, it supports forecasting and demand planning, aiding in accurate production scheduling and reducing lead times.
How manufacturing ERP works?
Manufacturing ERP systems work by integrating and automating various functions across the manufacturing organization.
Firstly, the system collects and consolidates data from different departments, such as inventory, production, sales, and finance. Furthermore, it organizes this data into a centralized database, providing a holistic view of the manufacturing operations. Additionally, it enables efficient communication and collaboration among teams.
Secondly, the system automates key processes, such as inventory management, production planning, and scheduling. Moreover, it optimizes resource allocation, streamlines workflows, and reduces manual errors.
Thirdly, the system provides real-time visibility into various aspects of the manufacturing process, such as inventory levels, machine utilization, and order status. Additionally, it generates comprehensive reports and analytics, aiding in decision-making and performance monitoring.
Manufacturing process flow
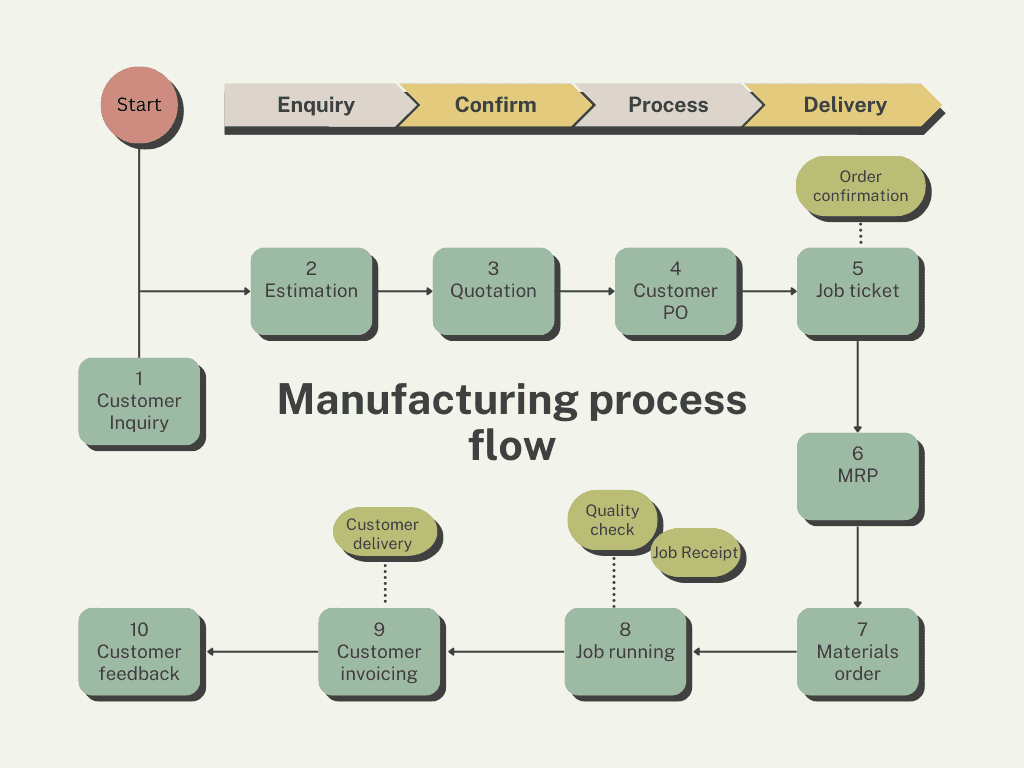
Customer Inquiry
The manufacturing process flow begins with a customer inquiry, where potential customers express their interest in a product or service. This inquiry serves as the starting point for gathering requirements, assessing feasibility, and initiating the manufacturing process.
Estimation
After customer inquiry, estimation plays a vital role in this flow by predicting resource requirements, production timelines, and costs. It involves analyzing historical data, market trends, and production capabilities to create accurate projections for successful planning and execution.
By providing insights into material procurement, production planning, and resource allocation, estimation ensures efficient utilization of resources, timely delivery, and cost-effective manufacturing.
Quotation
The quotation stage is a crucial step. Firstly, the customer’s inquiries are assessed. Secondly, a detailed quotation is prepared, considering factors such as materials, labor, overhead costs, and profit margin. Additionally, the quotation may include delivery timelines and terms of payment. The customer reviews and evaluates the quotation.
Customer purchase order
The manufacturing process flow begins with the receipt of a customer purchase order. This document outlines the customer’s requirements, including product specifications, quantities, and delivery dates.
Job ticket
The job ticket is a document that contains essential information about a specific production job. It includes details such as job name, description, materials required, quantities, instructions, and deadlines.
This document serves as a guide for workers, ensuring they have all the necessary information to execute the job accurately and efficiently.
Materials resources planning
Materials resource planning (MRP) is a key component of the manufacturing process flow. It involves determining the materials needed for production, their quantities, and timing. MRP calculates inventory levels, generates purchase orders, and ensures timely delivery of materials. By considering factors such as lead times, production schedules, and demand forecasts, MRP helps optimize inventory and prevent stockouts.
Materials order
In the manufacturing process flow, materials order plays a crucial role. It involves requesting and procuring the necessary materials to fulfill production requirements. This step ensures that the right quantity and quality of materials are available when needed, minimizing delays and disruptions.
Job running
In the manufacturing process flow, job running refers to the stage where a specific job or task is being executed. It involves actual production or manufacturing activities, such as assembling components, operating machinery, or performing specific operations.
Quality inspection
Quality inspection is an essential step in the manufacturing process flow. It involves examining products at various stages to ensure they meet predefined quality standards. Inspectors evaluate factors such as dimensions, functionality, and appearance to identify defects or deviations. Defective items are flagged for rework or rejection while conforming products proceed to the next stage.
Invoicing
Invoices include important details such as itemized prices, quantities, and payment terms. Invoicing ensures proper documentation and facilitates the financial aspect of the manufacturing process, allowing for accurate record-keeping and timely payments.
Customer delivery
It involves packaging and shipping finished products to customers. The products are carefully inspected for quality assurance before being packaged. Efficient logistics and supply chain management are crucial to ensure timely delivery.
Customer feedback
In the manufacturing process flow, customer feedback plays a crucial role in ensuring product quality and customer satisfaction. The customer feedback should be recorded for future reference.
How to align manufacturing process with ERP
Aligning the manufacturing process with an ERP (Enterprise Resource Planning) system involves integrating the system into the operations seamlessly. This can be achieved through various active smart actions, such as “integration,” “standardization,” “automation,” “optimization,” “real-time monitoring,” and “data synchronization.”
Firstly, integration entails linking the ERP system with different stages of the manufacturing process, such as Customer inquiry, estimation, quotation, etc. Secondly, standardization involves establishing standardized workflows and procedures across departments, ensuring consistency and efficiency.
Thirdly, automation plays a vital role by automating manual tasks and data entry, reducing errors, and enhancing productivity. Fourthly, optimization focuses on utilizing the ERP system’s capabilities to streamline processes, minimize waste, and maximize resource utilization.
Additionally, real-time monitoring allows for continuous tracking and analysis of key performance indicators, enabling prompt decision-making and proactive problem-solving. Lastly, data synchronization ensures that information flows seamlessly between the ERP system and manufacturing processes, enabling accurate planning, scheduling, and inventory management.
By aligning the manufacturing process with an ERP system, organizations can achieve improved operational efficiency, better inventory control, enhanced visibility, and the ability to make data-driven decisions, ultimately leading to increased productivity and customer satisfaction.
How to set up a manufacturing ERP system
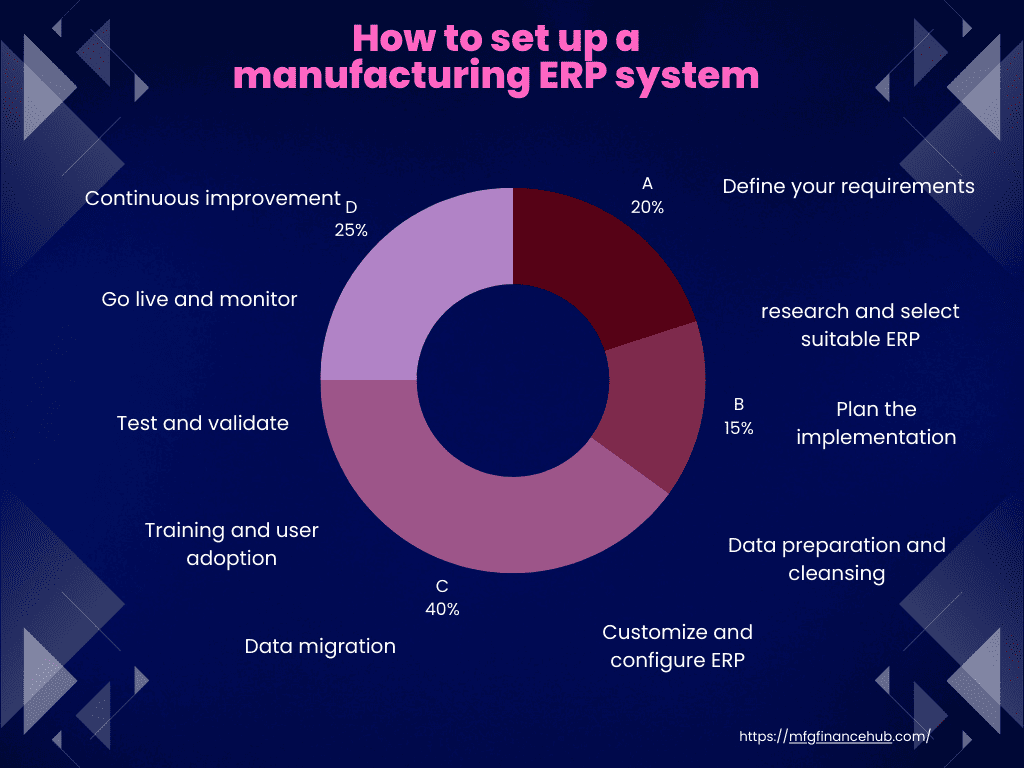
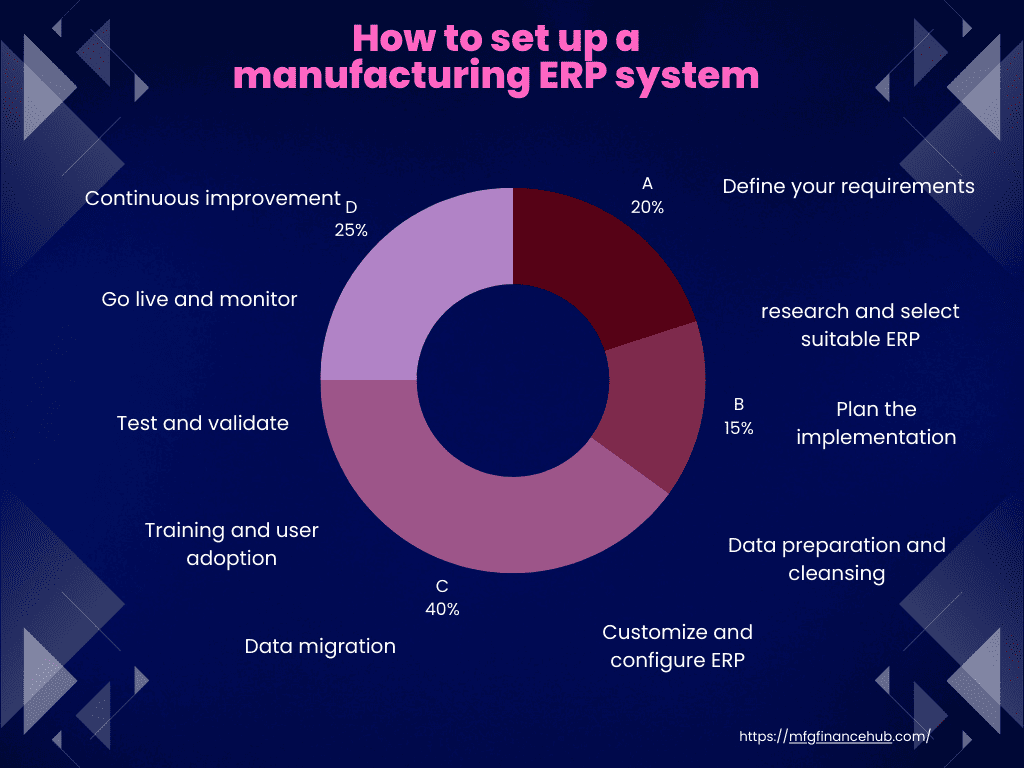
Define your requirements:
Determine your organization’s specific needs and objectives, and identify the areas of improvement, such as production planning, inventory management, supply chain, finance, HR, etc. Regulatory compliance, scalability, and integration with existing systems should all be taken into consideration.
Research and select a suitable ERP solution:
Make thorough research to identify ERP systems that meet your needs, evaluating factors such as functionality, industry-specific features, user-friendliness, support, and cost, and requesting demonstrations or trial periods from ERP vendors to evaluate their solutions.
Plan the implementation:
Create an implementation plan that outlines the steps, timelines, and resources required for the setup. Consider appointing a dedicated project manager who can oversee the implementation process and ensure effective coordination among different stakeholders.
Data preparation and cleansing:
In order to migrate data to the new ERP system, it is essential to clean and consolidate existing data, identify and correct any errors or duplicate entries, and set up rules for data entry and maintenance.
Customize and configure the ERP system:
Work closely with the ERP vendor or implementation team to configure the software to align with your business processes. Customize fields, workflows, reports, and user permissions based on your requirements. Ensure that the system is integrated with other critical applications, such as accounting software or CRM systems.
Data migration:
Once the system is configured, migrate your cleansed data from the old system to the new ERP system. This process requires careful planning to minimize data loss or corruption. Consider conducting trial runs or simulations to validate the accuracy and integrity of the migrated data.
Training and user adoption:
Provide comprehensive training to your employees on how to use the ERP system effectively. Train users from different departments on their specific roles and responsibilities within the ERP system. Encourage employees to provide feedback and address any concerns or questions they may have during the training process.
Test and validate:
Conduct thorough testing of the ERP system to ensure that all modules and functionalities are working correctly. Validate the system’s performance against your defined requirements and conduct user acceptance testing (UAT) to identify and resolve any issues or gaps.
Go live and monitor:
Once you’re confident in the system’s stability, go live with the ERP system. Monitor its performance closely during the initial period and address any unforeseen issues promptly. Establish a support mechanism to handle user queries, bug fixes, and system enhancements.
Continuous improvement:
An ERP system is an evolving tool. Regularly review and evaluate its performance, identify areas for improvement, and implement necessary updates or enhancements. Stay updated with the ERP vendor’s latest releases and take advantage of new features and functionalities.
Advantages of an effective manufacturing ERP system
- Enhanced Efficiency: ERP systems streamline operations by automating tasks, reducing manual errors, and improving overall productivity.
- Integrated Information: A centralized database allows for the seamless integration of data across departments, providing real-time visibility and facilitating better decision-making.
- Improved Planning and Scheduling: ERP systems enable effective production planning, resource allocation, and scheduling, optimizing workflows and reducing lead times.
- Inventory Management: Accurate tracking, forecasting, and demand planning feature aid in optimizing inventory levels, minimizing stockouts, and reducing carrying costs.
- Quality Control: ERP systems provide tools for monitoring and enforcing quality standards throughout the manufacturing process, ensuring consistent product quality and compliance.
- Cost Reduction: By streamlining processes, minimizing waste, and optimizing resource utilization, ERP systems help reduce operational costs and increase profitability.
- Regulatory Compliance: ERP systems assist in meeting industry regulations and standards, providing traceability and documentation for audits and inspections.
- Enhanced Customer Satisfaction: Improved production efficiency, on-time delivery, and better responsiveness to customer demands contribute to higher customer satisfaction levels.
- Data Analytics and Reporting: ERP systems generate comprehensive reports and analytics, enabling organizations to gain insights, identify trends, and make data-driven decisions.
- Scalability and Adaptability: ERP systems are designed to accommodate business growth and changes, allowing organizations to scale operations and adapt to evolving market conditions.
Also read: Top 6 manufacturing ERP software in 2023
[…] Read About: Manufacturing ERP system […]
[…] Manufacturing ERP systems automate and integrate processes, eliminating redundant tasks and enhancing operational efficiency. […]
ERP Software in Saudi Arabia